Newspapers and magazines in Europe are mainly based on papers manufactured from mechanical pulp and deinked pulp, so-called wood-containing papers. The most efficient deinking processes for these paper products are in an alkaline environment. Therefore, deinkability tests developed also assume alkaline deinking conditions.
INGEDE was the first and only association which established a deinkability standard for printed matter only. The first version of INGEDE’s deinkability test method 11 was published in 2001. In fact, there was a PTS method earlier which became even a DIN standard (withdrawn DIN 54606-1), but required always unprinted paper material for comparison reasons. So, deinkability tests of “unknown” print products derived from newsstands were not possible. INGEDE’s target was to develop an objective and easy to handle laboratory test method for testing the deinkability of a print product which simulates the behaviour of a print product as in an industrial alkaline deinking process. Because flotation deinking depends, amongst other things, on hardness of the utilised water, the procedure uses deionised water with a regulated water hardness, to avoid variations by using different local tap water quality. The developed test procedure was verified by comparing industrial deinking results with average values of numerous lab deinking tests with print product mixtures similar to industrial paper for recycling mixtures. A final pilot plant comparison was performed additionally with an identical paper product mix in lab scale and in the pilot plant of Escher Wyss in Ravensburg.
Over decades, the method was slightly adapted to product changes (e.g. increasing ash content of SC and LWC papers) or process observations made (e.g. pH value of virgin fibre based newspapers). During all that time, the method was based on an artificial ageing of the print product to simulate a natural ageing of about 3 months. Afterwards the process starts with an alkaline high consistency disintegration by addition of a constant alkaline deinking chemical recipe in a Hobart pulper, followed by a storage period and a flotation in the Voith Delta 25™ or the PTS flotation cell. Figure 1 shows a simplified sketch of the actual INGEDE Method 11.1
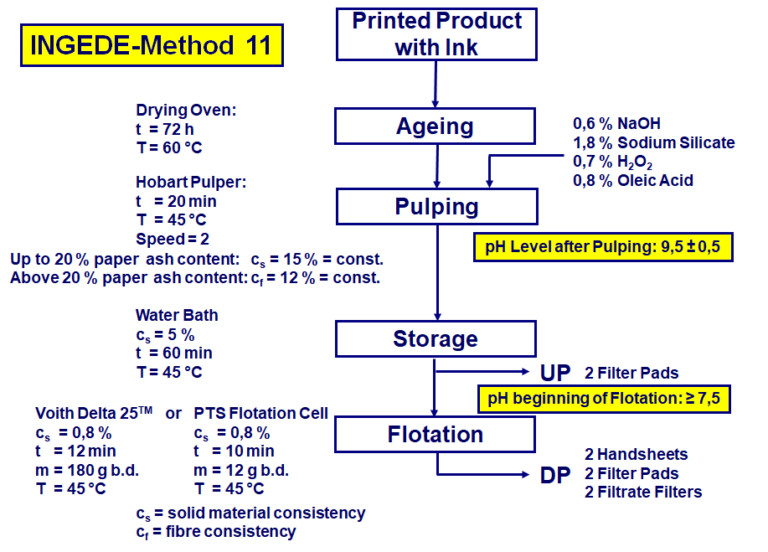
Before 2018, pulping was performed always under a constant solid material consistency of 15 %. But especially in coated papers the ash content (= mineral content) has been increased significantly in the last decade. Higher ash content of the paper results in a lower viscosity of the pulp and reduced shear forces in the pulper. The decreased shear forces may lead to insufficient ink particle fragmentation and coating colour flakes. So it was decided in the last adaption of the test method to adopt paper ash content above 20 % to a constant fibre consistency of 12 % during pulping. So before starting the test, the ash content of the print product at 525 °C has to be determined. Up to 20 % ash content pulping is performed at 15 % solid material consistency. Paper with exactly 20 % ash content has at 15 % solid material consistency a 12 % fibre consistency during pulping. Above 20 % paper ash content, pulping is performed with a constant fibre consistency of 12 %, resulting in an increasing product demand with increasing ash.
Since INGEDE Method 11 was first established, a set of additional methods exists for the preparation of the different test specimen and the parameters to be measured. Since the revision in 2014, all required information is comprised in the INGEDE Methods 1 and 2.2,3
Despite the fact that the INGEDE deinkability test method was well accepted on an international level, there was great interest in a higher standard level. With the DIN SPEC 55700 in 2016, a first step was taken for more internationalisation of INGEDE Method 11.4 One of the challenges was to describe the utilised equipment more openly, with required characteristics to avoid entitling specific manufacturers. Additionally, test sheet preparation and test parameters are added in this DIN SPEC, covering the complete procedure. The method is still valid, but actually has been surpassed by an ISO standard, described in the following paragraph.
The ISO 21993 deinkability test method was released in 2020 and is based on the DIN SPEC 55700.5 The method also contains the description of specimen preparation and test parameters. In some details the method is more precise than the DIN SPEC. The two largest differences are the following. First, pulping is performed independent from the paper ash content under a constant fibre consistency of 12 %. Second, the determination of further reflectance factors as R700 (see ISO 2469) or R950 (ERIC value, see ISO 22754) is no longer mandatory. When these values are not determined, the Ink Elimination (IE), which is one of the 5 parameters for the evaluation of the deinkability according to EPRC (European Paper Recycling Council) cannot be calculated. Then the final result, expressed as Deinkability Score, cannot be quoted.
For the sake of completeness, PTS Method RH 021/97 (Version: October 2012) should be mentioned.6 The method describes a recyclability test for printed graphic paper products (category I) and packaging materials (category II). Since the version of 2012 the deinkability test has to be performed according to INGEDE Method 11.
source link: https://forestbiofacts.com/
Case
-
Five Continents Special Paper 450,000 tons packaging paper Project
-
The i-CTMP High Yield Pulping Production line of Shan Ying
-
Shandong Tianhe i-BCTMP pulping line upgrade project
-
Guangxi Sun Cultural Paper
-
Qianan Boda Cultural Paper
-
Vietnam Thuận An Paper PM8 Project
-
EG-Paper Packaging
-
400t/d Bamboo Fiber i-CTMP Project
-
Guangxi Kebao ZDG425 Drum Pulper
-
The Rebuild of IKPP OCC Line