A scientific evaluation of the factors influencing deinkability has to consider the printing technology and the printing conditions. The results of the deinkability survey in Figure 1 give a general average overview. Detailed technical data of the printing process are not always available. In this average documentation of deinkability results, all relevant parameters are shown with its average positive or negative score. For example, in flexographic printing the parameters luminosity, ink elimination and filtrate darkening fail the test and for liquid toner printing dirt specks of both size categories are the critical parameter. In contrast, when the individual deinkability results are presented later, no positive deinkability parameters are shown if only one parameter did not reach the threshold.
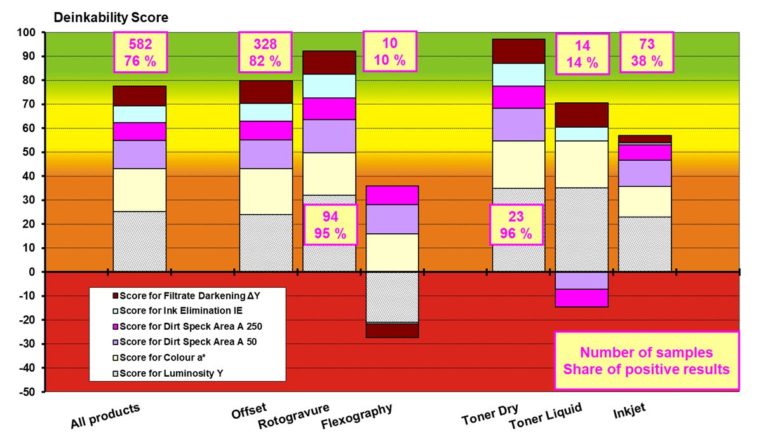
Each bar in Figure 1 shows the average Deinkability Scores grouped by printing technology. Three printing technologies – offset printing, rotogravure printing and dry toner printing – show good deinkability results on average with at least 82 % positive deinkability results per category. Three other – flexography printing, liquid toner printing and inkjet printing – are usually “not suitable for deinking”, with at least one of the assessment parameters receiving a negative score. In inkjet printing you find both good and insufficient deinkability, resulting in only 38 % positive test results. Nevertheless, no negative average score of a single parameter exists, indicating that for inkjet a number of different scoring parameters may fail in the test. When summing up the number of tests in the different categories it will not achieve the given number of all test results (582), because tested products may not belong to the categories shown here or are printed with more than one printing technology so that the result cannot be directly related to one category.
Figure 2 shows of the different printing processes the output in million euros of the European Printing & Printed Packaging for 2018, 2019 and a forecast for 2024 on basis of constant 2018 prices and exchange rates. Flexo is the single largest printing process (approx. € 40 billion) in 2018 and 2019, ahead of sheetfed offset with approx. € 30 billion. Flexo is mainly accounted for package and label printing, with corrugated packaging representing the single largest element. Future prospects look not-so-positive for almost every printing process due to the corona pandemic crisis. Referring to the printing processes relevant for graphic papers (sheetfed offset, heatset offset, coldest offset, gravure, electrophotography and inkjet) the output in 2019 is summing up to approx. € 107 billion, keeping in mind that at least for some of the listed processes the revenues are related partly also to packaging printing. But it becomes obvious that for graphic paper products, offset is the dominant printing process with a market share in Europe by value of about 57 %. Rotogravure had its peak of slightly above 20 % around the year 2000 and has continued declining since that time, reaching about 16 % in 2008 and about 8 % in 2019. The reason for this is the trend towards more and more specialised magazines with a smaller number of copies, which makes them uneconomical for rotogravure production. Other printing technologies, nowadays mainly digital processes, such as electrophotography and inkjet printing, account for a share of about 35 % of the value.
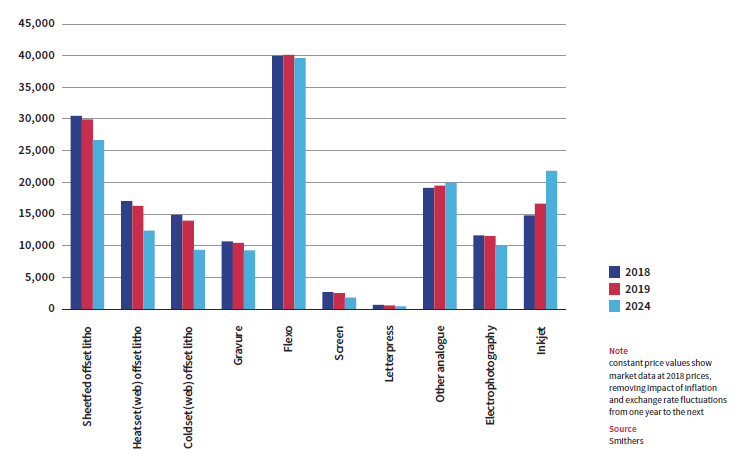
Source https://forestbiofacts.com/
Case
-
Five Continents Special Paper 450,000 tons packaging paper Project
-
The i-CTMP High Yield Pulping Production line of Shan Ying
-
Shandong Tianhe i-BCTMP pulping line upgrade project
-
Guangxi Sun Cultural Paper
-
Qianan Boda Cultural Paper
-
Vietnam Thuận An Paper PM8 Project
-
EG-Paper Packaging
-
400t/d Bamboo Fiber i-CTMP Project
-
Guangxi Kebao ZDG425 Drum Pulper
-
The Rebuild of IKPP OCC Line