Mixed post-consumer paper for recycling which is not thoroughly monitored during collection typically contains unwanted material and should be sorted before the recycling process. Sorting also adds value by enabling the sorting company to create higher priced qualities. After separating the mix into pure packaging and graphic grades, both of the resulting qualities have a higher market price than the mix. The output of a sorting plant often comprises of a small amount of mixed paper if it is not economical to divide the material completely due to the separation efficiency.
Theoretically, paper sorting doesn’t need any equipment and that’s how it began. More elaborate manual sorting plants consist of an elevated conveyor where the sorters stand on either side, grab the material what they have to remove from the main stream and drop it into chutes where it is collected in boxes underneath. These systems, common in Western Europe until the 1980s, were gradually equipped with more and more machinery.
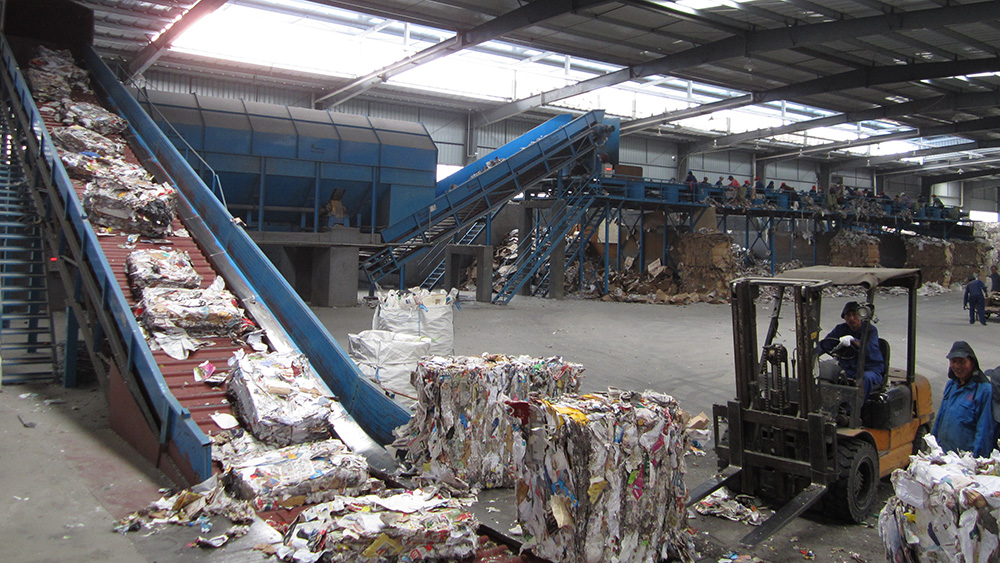
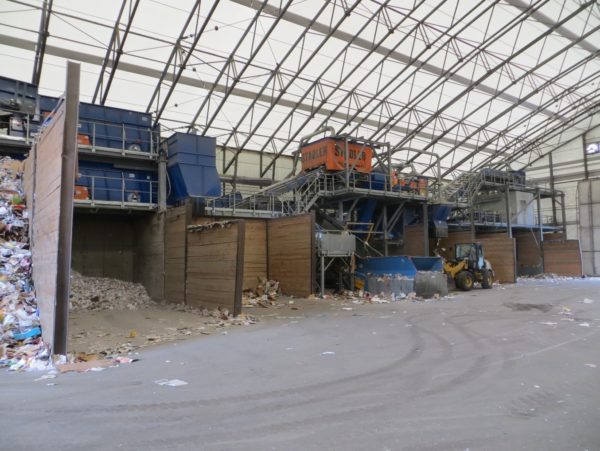
Today’s state of the art are automated systems consist of a coarse ballistic sorter to separate the large and stiff cartons, a fine ballistic sorter to remove small sized material, and an NIR sensor often combined with camera to detect non-paper material and unbleached paper and board products. A subsequent air jet array blows the detected material off the main stream. At the end of the line there is often a cabin for quality control and final manual sorting.

Figure 1 depicts a state of the art sorting plant and Figure 2 the materials of it. From the input on the very left the paper passes the two ballistic sorters (blue, mounted on top of each other), continues to a metal separator and the NIR sensor (orange) and finally reaches the sorting cabin. The output material (small pictures in Figure 6, clockwise) is the rather undefined fine fraction, the packaging board, the graphic paper, and mixed paper. The latter is a small stream of the total since a complete separation is often not economical.
It is normal that the operation of a sorting plant is adjusted to the local or current market conditions. For example, if you need a high purity of the graphic portion, you decrease its output and create more mixed paper – and vice versa.
Depending on the input and on the output compositions and qualities, there are various plant designs, in general getting more complex with an increasing number of different input materials.
If there is non separate collection at all and all household waste is in the same receptacle, the paper fraction in it is often wet and maybe rotten with the consequence of being unusable in the paper industry.
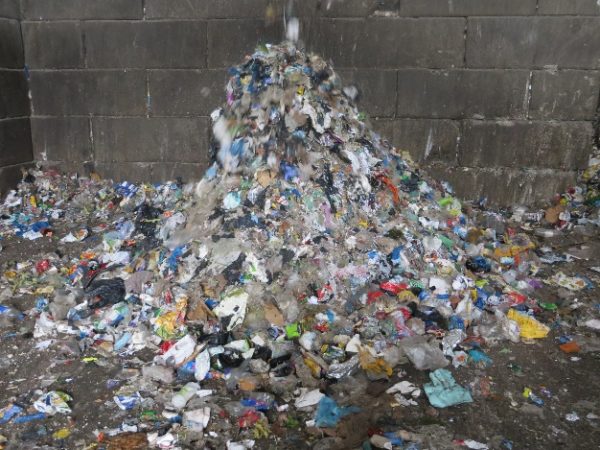
A commingled collection of recyclables is convenient for citizens because they do not have a difficult task in separating. Also, the collection itself is relatively easy but the necessary subsequent sorting has to be more elaborate and the quality of the resulting paper fractions can be questionable. Commingled collection can be paper, plastics and tin with glass, typically in the United Kingdom, or without glass as it is widespread in France. Additional concepts exist as well, e.g. collecting the recyclables in two fractions – dry and potentially wet.
Table 1. Examples for selectivity of recyclables in common collection systems

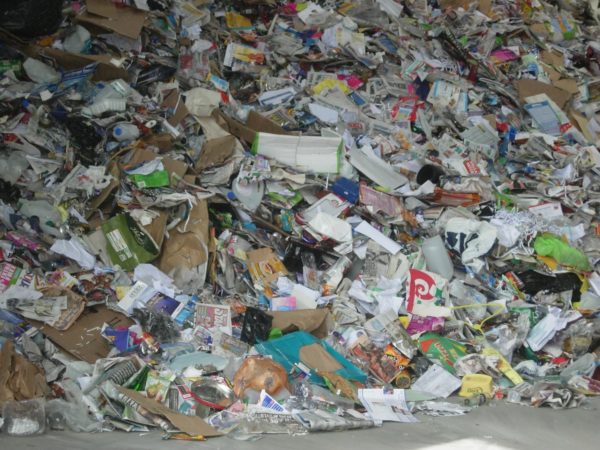
Commingled collection requires a sophisticated sorting afterwards in a so-called “Materials recycling Facility” (MRF). This is not only costly but is also subject to separation efficiency. Particularly with commingled collection, there is a either danger of a high content of non-paper components after sorting or of low yield.
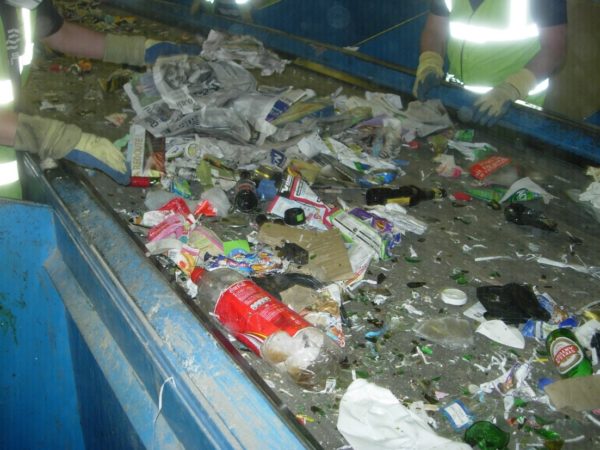
Figure 5 gives an idea of the issue. It shows the reject conveyor of a MRF. The high amount of partially broken glass is visible. Since the broken glass is detrimental to the recycling process, the yield of the paper fraction has to be reduced, requiring a manual sorting to recover the paper in the reject.
In regions with a developed system of paper collection, a separate collection of paper and board products is common. The material from it is mixed paper and this is often sorted to remove impurities and to increase its value by splitting it into a packaging and a graphic stream as well as a small stream of mixed paper since the complete separation is often not economical.
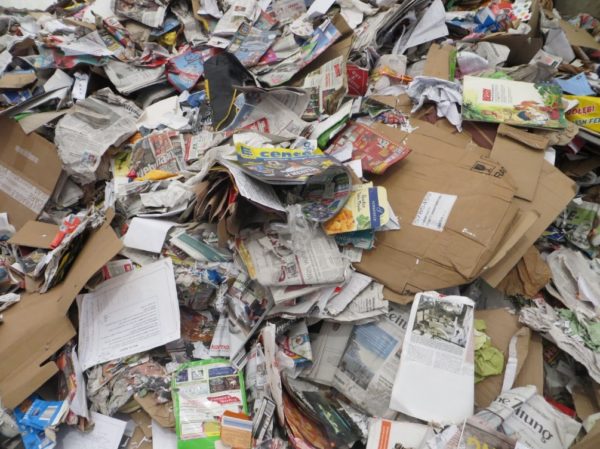
The best post-consumer qualities can be achieved by a selective collection, at which graphic and packaging paper products are collected separately from each other.
source link: https://forestbiofacts.com/
Case
-
Guangxi Qingyun Tissue Paper project
-
Gansu Yusen Tissue Paper
-
Five Continents Special Paper 450,000 tons packaging paper Project
-
The i-CTMP High Yield Pulping Production line of Shan Ying
-
Shandong Tianhe i-BCTMP pulping line upgrade project
-
Guangxi Sun Cultural Paper
-
Qianan Boda Cultural Paper
-
Vietnam Thuận An Paper PM8 Project
-
EG-Paper Packaging
-
400t/d Bamboo Fiber i-CTMP Project