The deinkability assessment according to EPRC (European Paper Recycling Council) sets targets and limits for the evaluation of the deinkability of a print product and is based on the results of INGEDE Method 11.1 In total, five parameters have to be determined for the assessment of the deinkability (Figure 1). Three parameters characterise the deinked pulp (DIP) quality. Luminosity Y gives information of the brightness, the a*-value describes a colour shade on the red-green-axis and the dirt speck area A specifies the cleanliness of the deinked pulp. Dirt speck area is determined in two size classes, comprising all visible specks above 50 µm equivalent circle diameter and separately the large specks with a diameter above 250 µm for the most disturbing particles. The two last characteristics determined are the process parameters Ink Elimination (IE) and the discoloration of the filtrate (ΔY). The results of the single parameters give the experts an indication in which direction a print product has to be improved to pass the test or which problems are to be expected when large volumes of such a print product enter a commercial deinking line.
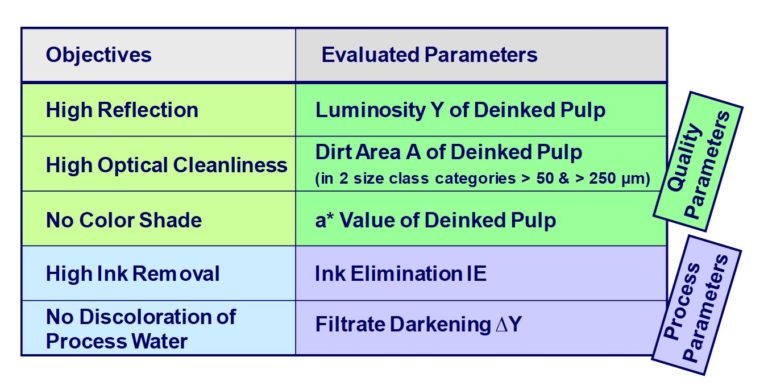
The EPRC deinkability assessment converts the deinkability results of INGEDE Method 11 into a deinkability score. Therefore, one of the 5 print product categories has to be selected: newspapers, coated or uncoated magazines, and low ink coverage products. Low ink coverage products are subdivided below and above a brightness level of 75 % of the unprinted base paper and are defined as products which are typically printed on high-grade paper and/or with significantly lower ink coverage than magazines. This category includes text-only prints, transactional and transpromotional prints, formal or personal correspondence, one-side printed products, low ink coverage books and the like. For further definition and examples of the print product categories see the ERPC document.1
The scoring system allows the expression of the deinkability assessment in terms of one figure by weighing the parameters according to their importance. Additionally, the deinkability scores provide the opportunity for cross comparisons between different product categories. The maximum score is 100 points in all product categories. Due to the fact that according to INGEDE Method 11 the flotation time is relatively long in the test, the results are close to hyperflotation, meaning that particles which can be floated have been floated. Therefore, it is important for those comparisons that the flotation yield is in a certain range. INGEDE Method 11, as well as EPRC scorecard, set a minimum flotation fibre yield of 65 %. If the fibre yield is below 65 % the flotation test has to be repeated with a reduced flotation time, typically resulting in higher yield and somewhat poorer optical deinking results.
To achieve a common point system, threshold as well as target values are defined. Depending on the type of threshold values either a lower threshold, an upper threshold or a threshold corridor is fixed which have to be exceeded, undercut or met respectively. The threshold values for newspapers, coated or uncoated magazines and low ink coverage products with a brightness of the base paper ≤ 75 % are independent of the print product categories and are listed in Table 1. Low ink coverage products with a brightness of the base paper > 75 % are typically used by deinkers to produce a higher quality of deinked pulp. Therefore, the lower threshold value for luminosity Y is higher with 67 instead of 47 (Table 2). All other parameters are on the identical level. For a given print product, threshold values have to be fulfilled for each parameter. If one or more threshold levels are not reached, a print product is judged as “not suitable for deinking”.


According to Table 3 target values of the parameters colour shade (a*-value), dirt speck area (A50 and A250) and filtrate darkening (ΔY) are equal for each print product category. The target values of the luminosity of the deinked pulp (Y) and the Ink Elimination (IE) have differing levels depending on the print product category.
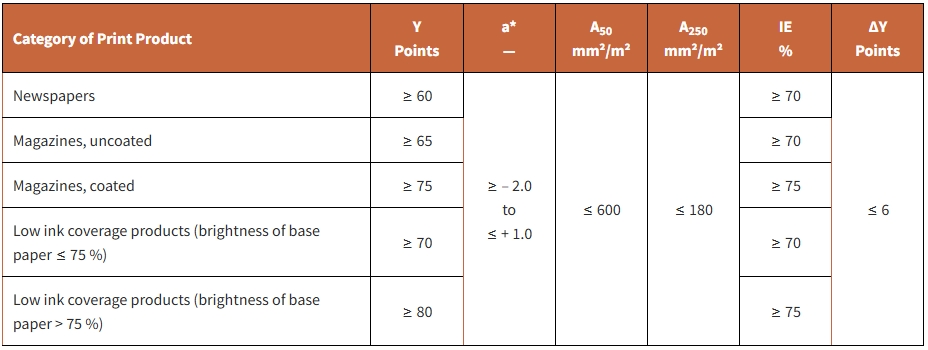
If the target value of a parameter is met, the full score is given for this parameter. The scores of the six parameters in Table 4 have different values in order to reflect their importance. The DIP quality parameters have the largest impact on the total deinkability score with a proportion of 35 % for the luminosity, followed by the dirt particle areas (25 % as total of A50 and A250) and colour (20 %). The process parameters ink elimination and filtrate darkening contributes each to 10 % only.

Between the threshold and the target value of each parameter, the score is linearly subdivided, resulting in a constant increment per parameter. Finally, the score of all five parameters is added up to provide a single number that corresponds to the total score for a particular print product. This allows a simple overall assessment on the deinkability of a print product with one numerical value between 0 and 100 points comparable to test results of consumer goods (Table 5). If one or more threshold values fail, the print product is considered unsuitable for deinking. Nevertheless, the product may be well recyclable without deinking – for example in a board mill. If all thresholds are reached the product is judged to be deinkable with three various gradations: poor, fair and good. An easy to handle deinkability score calculator is available from the EPRC website named “Assessment of Print Product Recyclability – Deinkability Score – Calculator”.2
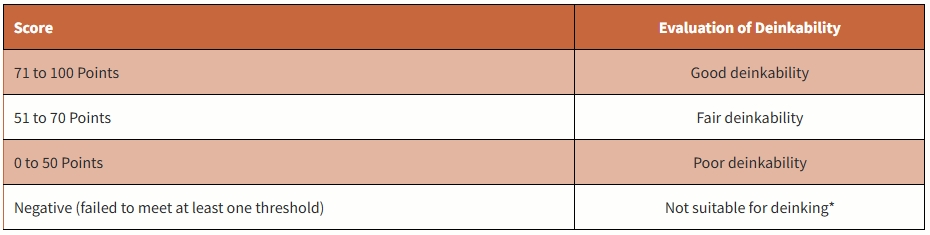
*The product may be well recyclable without deinking
Today, the majority of printed products is deinkable and will pass the deinkability test. Therefore, the EPRC document 1 has formulated in its annex exemptions from testing of some printing technologies and material combinations with sufficient experience. There is enough confidence that these products will deliver good deinkability results. The following printed products are exempted from the laboratory deinking test procedure under the given boundary conditions and will be considered as suitable for deinking according to the EPRC scorecard:
- Graphic products printed in heatset offset presses on coated paper, provided that the ink composition is according to the following specification:
- 10 – 25 % pigments
- 20 – 48 % rosin-based resins and hydrocarbon resins
- 25 – 45 % high boiling mineral oils (boiling range 250-310 °C)
- < 10 % oxidative drying oils (e.g. vegetable and modified vegetable oils)
- 1 – 12 % additives.
- Graphic products printed in rotogravure presses on coated or uncoated paper provided that no soluble dyes were added to the ink and its composition is according to the following specification:
- 5 – 10 % pigments
- 15 – 30 % rosin-based resins and hydrocarbon resins
- 30 – 70 % toluene
- 3 – 5 % additives.
If a printing technology or a material combination is not listed in this annex, it does not allow any conclusion about its deinkability behaviour. It means that more experience is needed to be gathered to be exempted. Print products containing any parts where inks or varnishes are cured with radiation technologies, e.g. UV, are not exempted from the laboratory deinking test procedure.
Source https://forestbiofacts.com/
Case
-
Five Continents Special Paper 450,000 tons packaging paper Project
-
The i-CTMP High Yield Pulping Production line of Shan Ying
-
Shandong Tianhe i-BCTMP pulping line upgrade project
-
Guangxi Sun Cultural Paper
-
Qianan Boda Cultural Paper
-
Vietnam Thuận An Paper PM8 Project
-
EG-Paper Packaging
-
400t/d Bamboo Fiber i-CTMP Project
-
Guangxi Kebao ZDG425 Drum Pulper
-
The Rebuild of IKPP OCC Line