When we are talking about producing high quality tissue paper, most of the people will firstly have the "crescent-shaped forming technology" in their minds, well, it is saying stock preparation contributes 70% to the quality of the final product and paper making contributes the remaining 30%, a good forming of the fiber mat on the tissue machine can never leave the precondition that the stock has be well and scientifically prepared.
As a stock preparation system supplier, Yunda provides systematic solutions for the tissue machines and has supplied as much as 86 stock preparation and approach flow systems to different customers all over the world in between 2016 and 2022. Yunda i-TSP stock preparation has superior performance in reducing energy consumption, controlling product cost, improving product quality and operation stability.
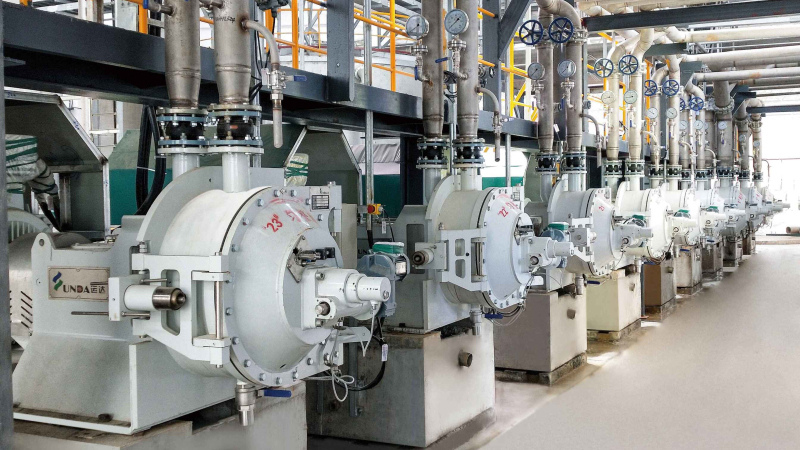
Pulp bales go firstly to the auto de-wiring machine with a conveyor from where the wires will be cut and removed automatically, after that they go into the mid-consistency pulper, under the mechanical force and hydraulic force generated by the rotating rotor the bales will be fully slushed into a constant consistency and will be then fed into the dump tower through a discharge pump. Pulping process can either be in a batch way or in a continuous way. In the dump tower pulp will be well swelled and then it goes to the refining system for the development of the fiber strength. HD Cleaning and Magnetic Separation will be need before entering the refiner to remove the heavy and hard contaminants and protect the refiner plates. After the refining process with required beating degree the pulp will be then fed into the final storage tower. Afterwards in the mixing process different furnishes will be dosed into the mixing chest automatically as per the setting, from the mixing chest the mixed pulp travels through a mixing refiner, machine chest, fan pump, screen and finally reaches the headbox.
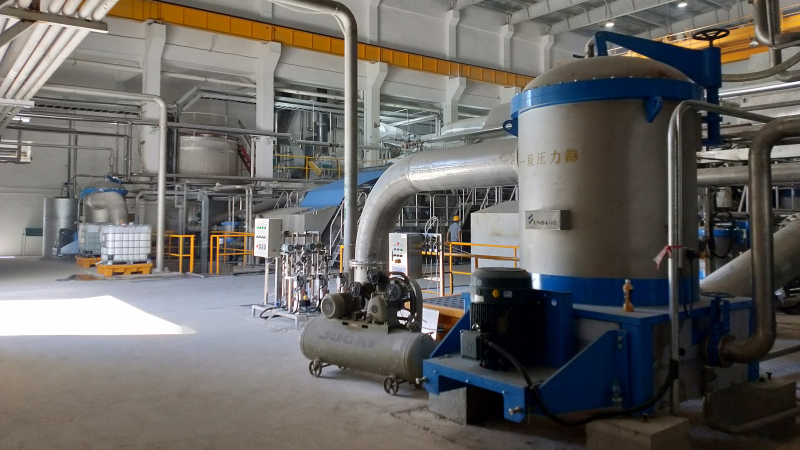
Advantages:
A. Long fiber, short fiber and broke are treated separately, Using different refining and deflaking equipments to ensure high efficiency, low energy consumption, and high bonding strength of the final paper .
B. Equipped with an automatic de-wiring machine to reduce labor intensity, and save labor costs.
C. S-type medium consistency pulper rotor with intelligent pulping control system saves approx 30% of the energy consumption when compared to the conventional pulper.
D. The combined use of Metal Separator and HD Cleaner has a higher removal efficiency of destructive heavy contaminant.
E. PM double disc refiner provides low idle power, high reliability and energy conservation, and high quality of beating.
F. NLS inflow screen provides low pulsation, low energy consumption and excellent paper-forming evenness.
The system is built with automatic feeding, intelligent pulping, switchable intermittent and continuous pulping modes, and the fixed specific energy consumption for refining, it has multi advantages like high automation, low energy consumption, reliable runnability, and low maintenance costs.
Case
-
Five Continents Special Paper 450,000 tons packaging paper Project
-
The i-CTMP High Yield Pulping Production line of Shan Ying
-
Shandong Tianhe i-BCTMP pulping line upgrade project
-
Guangxi Sun Cultural Paper
-
Qianan Boda Cultural Paper
-
Vietnam Thuận An Paper PM8 Project
-
EG-Paper Packaging
-
400t/d Bamboo Fiber i-CTMP Project
-
Guangxi Kebao ZDG425 Drum Pulper
-
The Rebuild of IKPP OCC Line