The recycled cartons are compressed and packed into cubes for the convenience of transportation, and then sent to recycling plants.
The cardboard boxes are recycled and made into recycled paper.
Generally Speaking, the treatment of waste paper includes four stages of pulping, screening, cleaning and thickening.
However, due to the variety of impurities contained in waste paper, especially the application of plastics, hot melts and other synthetic materials on paper products, the screening and cleaning section in waste paper treatment process is complicated. Therefore, screening and cleaning has become a key issues in recycle fiber stock preparation process.
In this way, the entire waste paper stock preparation process divides into two parts: pulping and cleaning.
Tips:The deinking of ink-containing waste paper is a special requirement in recycle fiber stock preparation process, which needs to add the deinking and bleaching processes.
How to make waste paper into paper pulp?
I-OCC Stock Preparation System
link: https://www.yundapm.com/solutions/i-occ/
1. OCC Recycled Fiber Technology
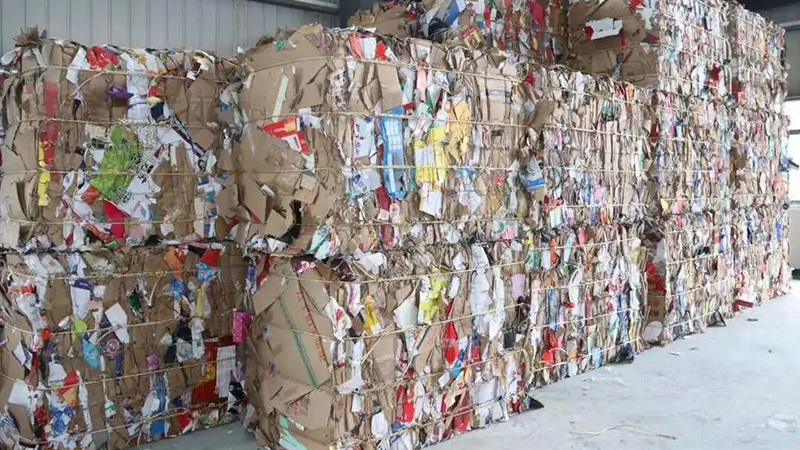
OCC/mixed waste paper main components :
- Fiber and Debris ,Ash.
- Rejects( Plastics,Wires & Strings,Metals,Non-Ferrous Metals,Sand, Stone & Glass,Stickies...)
In OCC Stock Preparation:
- To Retain as much Fiber as possible (High Yield);
- Typical System Losses: Fiber ≤2.8%, Debris ≤6.5%;
- To Retain certain amount of Ash;
- To Remove as much Rejects as possible;
- Typical Stickies Removal Efficiency: ≥90%;
Proper Reject Sorting and Treatment is not only a way of being Environmental Friendly but also Brings good Margins…
For Details of the Reject Handing System please Contact Yunda!
The general process
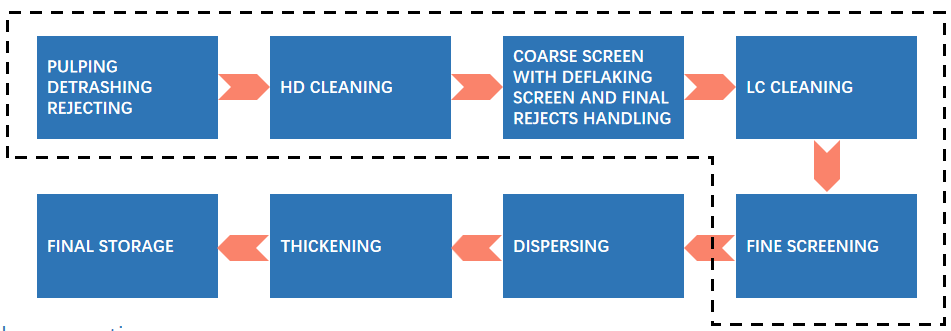
i-OCC stock preparation system
Yunda i-OCC stock preparation system has the advantages of high yield, high quality, high reliability and low energy consumption. The system realize the idea of less intermediate stock chests, which can save appx. 20% of the floor spaces; using of the eco-jet mixing technology provides lower investment, lower energy consumption and lower maintenance cost; group start / stop provides easy operations.
The waste paper after bale breaking goes evenly into the Drum Pulper with less hits, accelerated water absorption and increased pulping efficiency. with fully disintegration by rubbing, The stock will be diluted to a lower consistency of 3 - 5% by the spraying water coming out of the shower pipe in the screening section. The accepted stock goes through the screen holes. And the impurities such as waste plastics are discharged from the reject end. The stock in the bottom vat of the Drum Pulper is pumped into the Two Stages HD Cleaner,the accept from the 1st stage goes into the Dump Tower and the Reject is collected in the Settling Tank and will be pumped from the top to the second stage for further cleaning. Accept of the 2nd stage is led back to the Pulper and the heavy contaminants is dumped to the sand separator to collect the sands from water.
The stock after the Dump Tower is pumped into the Coarse Screening System, Reject of the first stage goes to the 2nd stage via one eco-jet mixer directly, And reject of the 2nd stage goes further though a Float Purger and a Reject separator, finally the light impurities collected for further treatment. Accept goes to the fractionation system and after that short fiber goes after thickening to the storage tower.
Long fiber enters the LC Cleaner plant in 4 stages design; light particles was removed by centrifugal forces; In the fine screening stage Oda screen basket provides high stickies removal efficiency, high throughput, and energy-saving; The final stage of the fine screen has additional under the rotor dilution which helps to either reduce excessive thickening of the reject inside the screen basket or clean the impurities completely, accepts from different stages are all going forward and combined together and fed into the Long Fiber Disc Thickener.
The long fiber mat is knocked off by the knock-off shower and then enters the Disperser through Screw Press, Plug Screw, Shredding Screw, Heating Screw for further treatment. after that the stock is conveyed to the long fiber storage tower and will be further refined by the Double Disc Refiner, Yunda PM Double Disc Refiner is reliable, energy-saving and high quality of beating.
i-OCC is not only good in stock preparation but also good in reject handling, which it provides human-machine harmony, green and environment friendly, and is the priority for OCC treatment.
Typical flow occ line, conventional pulping
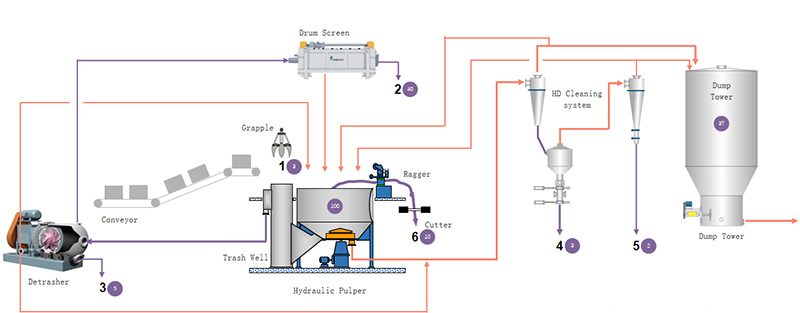
Light Rejects: 1, 2 ; Heavy Rejects: 1, 3, 4, 5 ; Rag: 6;
2.i-OCC Systems & Equipment
Hydraulic pulping system
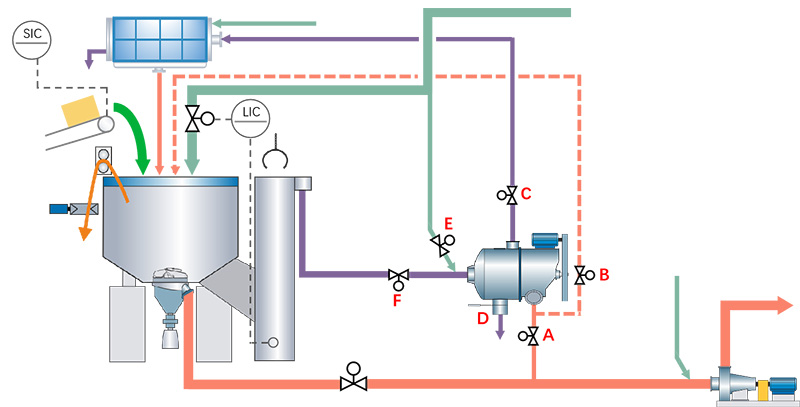
D-Shaped Hydraulic Pulper
A | B | C | D | E | F | Duration | |
Extraction | O | C | C | C | C | O | 8 min |
Defibering | C | C | C | C | C | O | 2 min |
Washing I | O | C | C | C | O | O | 15 sec |
Washing II | O | C | O | C | O | C | 60 sec |
Washing III | C | O | O | C | O | C | 60 sec |
Rejecting | C | C | O | C | O | C | 75 sec |
Heavy Rejecting | C | C | C | O | C | C | 5 sec |
O=Open; C=Closed;Total Sequence Time is 13.5 min; |
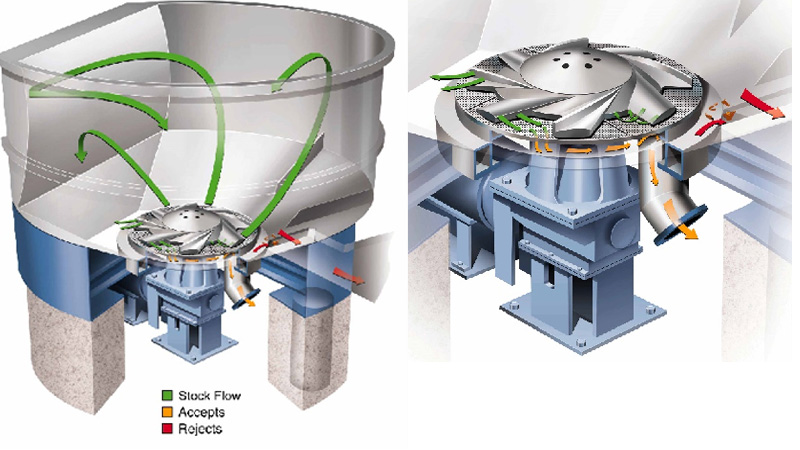
D-Shaped vat design allows smaller vat and lower power requirements for a given application:
- Lower initial capital investment;
- Less floor space requirements;
- Better auxiliary equipment layout;
- Lower operating costs;
- Quicker return on investment;
“R” Raised rotor design provides:
- Better heavy rejects handling;
- Better rag rope operation;
- Longer rotor and extraction plate wear life;
Extended and large hole extraction plate provide:
- Maximum extraction open area and hydraulic capacity;
- Low extracted stock velocity;
- Low the discharge time;
- Less rag breakdown;
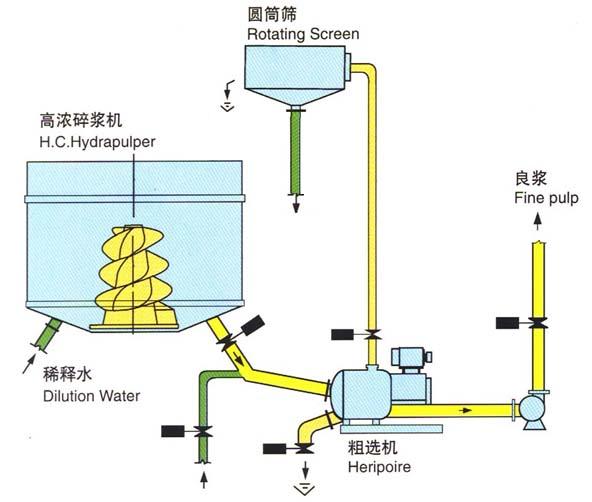
Yunda high-consistency pulper realizes bleaching while pulping at a consistency of 12-18%.
This technology speeds up the bleaching effect, saves the amount of bleach dosage, reduces the power of the pump and the consumption of heating steam.
It means that the pulp is bleached with a chlorine-free bleaching agent under medium consistency conditions, and the consistency of the pulp is increased as much as possible within an appropriate range and the temperature of the pulp is lowered.
Detrasher
- Deflaking efforts;
- Minimum fiber loss;
- High reject load permitted;
- No separate pump is needed;
- Less maintenance requirement;
Super Screen (For 1st & 2nd Stage Coarse Screen)
- Up streaming, heavy rejects will be removed from the bottom directly;
- Reduced wearing, reduced power consumption;
- Light Material, such as Styrofoam, rises naturally through screening zone to reject stream;
- Highest accept cleanliness;
- High yield;
- Defibering of remaining flakes in the stock from the pulper;
- No size reduction of contaminants;
- High reject consistency;
- Low maintenance cost;
Fiber Sorter (For 3rd Stage Coarse Screen)
- Deflake flakes to prevent loss of usable fiber; Deflaking efficiency up to 80%;
- Hydraulic separation of contaminants from flakes and fiber;
- Concentrate contaminants for tailing unit;
- Continuous light reject flow;
Reject Sorter(For 4th Stage Coarse Screen)
- Deflake flakes to prevent loss of usable fiber;
- Simple operation;
- No pressure;
- No fiber in the reject;
- Fit for various capacity;
- Simple operation;
- Simple piping;
Drum Screen
- For reject washing, to save fiber further;
- Fiber free in the discharge reject;
- Efficient light rejects removal;
- Less maintenance requirement;
Drum pulping system
Drum pulper - gentle pulping principle
Gentle defiberizing of furnish with specially shaped internals
Lifting plates in staggered arrangement = constant, smooth stock falling and tumbling;
Stock moves slowly towards the screening section due to the drum declination;
- No Cutting Forces, No Aggressive Shearing;
- Minimum Breakdown of Contaminants;
- Maximum Retention of Fiber Physical Characteristics;
- Lowest Power Consumption;
- Minimum Maintenance Requirements;
- Excellent Quality Stock;
- Enables All Grades of Recycled Furnish;
- Continuous Operation & Trouble Free Production;
High density cleaning system
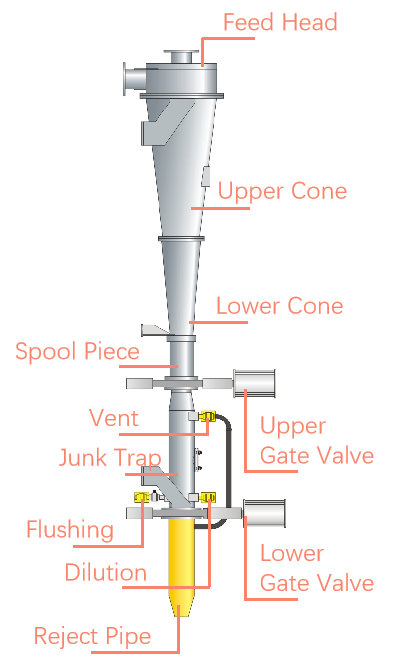
High density cleaner
- 2 Stage system with sedimentation tank for heavy rejects(>1 mm);
- Removal by centrifugal forces;
- Separation of particles with higher density than fibers;
- High remove efficiency for heavy reject;
- Protect coarse screen basket;
- Ceramic inlet cylindrical section;
- Ceramic cone;
- “Rotation break”;
- Fiber saving back-flush water;
- Periodic discharge for low fiber loss;
3.How is pulp turned into paper?
Forming dehydration
Dispersing the pulp evenly is an important part of turning the pulp into paper that meets the requirements of use, this needs to dilute the pulp to a consistency of 0.3%~1% to make the fibers more evenly dispersed, and then sprays the pulp evenly onto the forming wire through the headbox, and dehydrate through the gravity and vacuum of the wire part reach 20 % dryness.
Press dehydration
Paper sheets with a dryness of about 20% need to be squeezed by press rollers to further remove moisture. Generally, they will go through 2~3 times of pressing to reach a dryness of about 50%.
Drying
After the initial pressing and dehydration, in order to allow the water to evaporate quickly, it needs to be dried by high-temperature steam, and the high-temperature steam is sent into the steel roller (drying cylinder), and the surface temperature of the drying cylinder is transferred to the wet paper sheet, so that the paper sheet Moisture drops below 10%.
Rolling
The last step in the utilization of waste paper is to roll the paper into a roll with a roller using friction force, and then produce different types of paper according to different needs.
Finished product
The processing plant will purchase base paper for processing according to the end use, These papers will be processed into cartons, packaging bags, packaging boxes, etc. used in daily life through different processing methods such as printing, coating, laminating, bronzing, die-cutting, and box-gluing.
How to deink and bleach waste paper pulp?
For higher quality paper such as writing paper and tissue paper, the waste paper recycling process also includes deinking, bleaching and other processes.
This technology is suitable for enterprises that use waste paper as raw material to produce deinking pulp.
Waste paper deinking technology mainly refers to the characteristics of ink, Through the action of chemicals, mechanical force and heating, etc., the adhesion of ink particles to fibers is destroyed, and the printing ink particles are separated from the fibers and separated from the pulp.The deinking method is divided into flotation method and washing method. The advantage of flotation to remove ink particles is less fiber loss and less waste water. The deinking method in the washing method is relatively clean, with low ash content, convenient operation, stable process, low power consumption, and low equipment investment; but the water consumption is large, the fiber loss is large, and the yield is low.
4.i-OCC Major Installations & References
Jiangsu Jintian
Zhejiang Jinli Paper Project
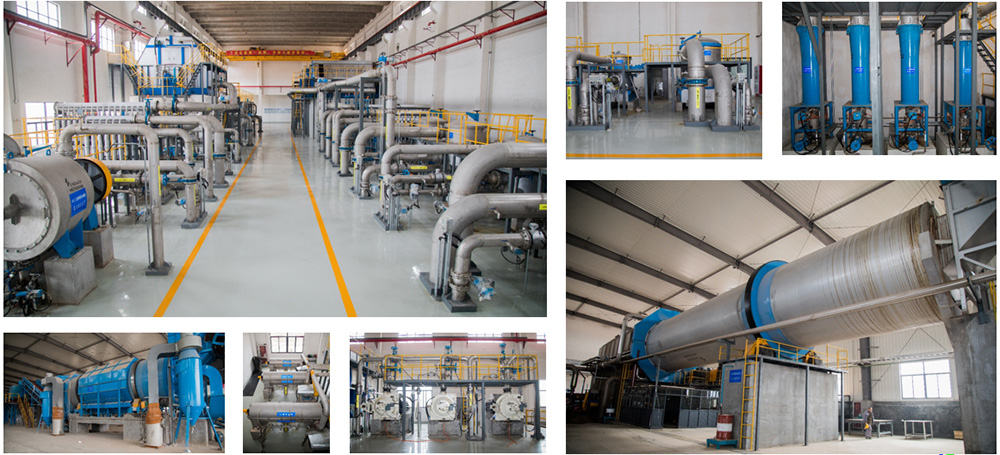
Case
-
Five Continents Special Paper 450,000 tons packaging paper Project
-
The i-CTMP High Yield Pulping Production line of Shan Ying
-
Shandong Tianhe i-BCTMP pulping line upgrade project
-
Guangxi Sun Cultural Paper
-
Qianan Boda Cultural Paper
-
Vietnam Thuận An Paper PM8 Project
-
EG-Paper Packaging
-
400t/d Bamboo Fiber i-CTMP Project
-
Guangxi Kebao ZDG425 Drum Pulper
-
The Rebuild of IKPP OCC Line