For graphic paper products deinkability is in the focus of a recyclability test. Nevertheless, repulpability has to be ensured as a prerequisite for a deinking test. Graphic paper products typically have no problems with repulpability and the yield of the pulping process is not determined especially. In contrast, packaging paper products can behave completely different during repulping and there the reject mass is determined separately. Because graphic and packaging paper for recycling is treated typically under different industrial pulping conditions (graphic paper for recycling: high consistency pulping with chemicals / packaging paper for recycling: low consistency without chemicals), laboratory recyclability simulations have to consider this particular situation.
Deinking is the most important process stage in processing paper for recycling as a raw material for the production of deinked pulp (DIP) primarily used for manufacturing new graphic papers, hygienic papers, or white top layers of packaging paper and board. Deinking is the process for removing printing inks from a pulp slurry to improve optical characteristics of pulp and paper using printed raw materials. Deinking is done in two phases: detaching the ink from the fibre surface and separating the ink from the pulp slurry. The first phase takes place during repulping and is a function of the print product i.e. paper grade, printing technology, finishing, age, etc., and the chemical as well as the mechanical process conditions. The detached ink particles are then removed by flotation or washing (see also section Unit operations and equipment in recycled fibre processing).
The term “deinkability” refers to the ability of a printed product to be deinked and is defined as: “Removability of ink and/or toner from a printed product to a high extent by means of a deinking process. This shall restore as well as possible the optical properties of the unprinted product”.1
Deinking by flotation is the predominant technology used in Europe, Asia and North America. Deinking by washing is and will remain limited to special products such as hygiene papers due to a better removal of minerals. For both processes, ink detachment from the paper surface is a prerequisite for a good deinking result. Cross-linked and vegetable oil based inks are harder to detach than mineral oil, solvent or water based inks. For a flotation process to be efficient, the printing inks must have certain additional specific characteristics. They have to be hydrophobic and need to be in a certain particle size range in order to be suitable for flotation Figure 1. As a rule of thumb, the suitable particle size ranges from about 10 µm to 100 µm.2 In fact, the range is significantly larger; with at least reasonable effectiveness in a minimum range of 5 to 10 µm up to a maximum range of 250 to 500 µm.3 Other publications suggest similar ranges, but without providing evidence of how the data were achieved.4 The exact limits also depend on the hydrophobicity and the rigidity of the ink particles as well as the geometry of the particles. Further essential prerequisites for the efficiency of flotation deinking are the proper hydrodynamic conditions.5 Construction and operating parameters of the flotation equipment have to take care of those.
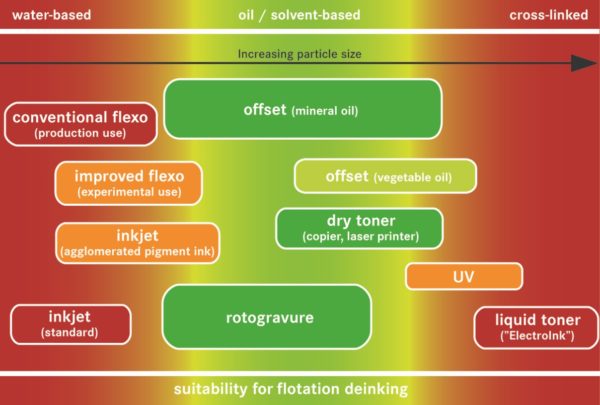
Figure 2 shows some handsheets of deinked pulp to demonstrate different results of deinkability. On the left examples of water-based flexographic newspaper, in the centre a good deinkable offset newspaper with mineral oil based inks and on the right hand side on top an offset newspaper with vegetable oil based and too many ink specks and at the bottom a digitally printed newspaper based on woodfree paper with UV-cured preprint.
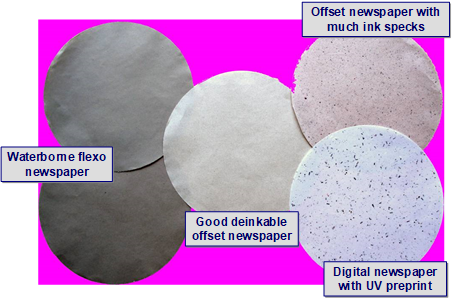
Wash deinking is not sensitive to the physico-chemical properties of the ink. The ink particles have to be detached from fibres but do not require any specific surface chemistry. An important characteristic of deinking by washing is the fact that the process removes all particles from the pulp which are below a size of about 40 microns 8. This includes fines and minerals (fillers and coating pigments). High quality hygiene papers or mills producing pulp substitutes need a deinked pulp with low mineral content. These mills operate washing stages, mostly in addition to flotation. In most deinking installations it is desirable to retain fines and minerals to a high extent. In these cases the low yield is prohibitive for a feasible operation.
Ink pigments are of very low particle size below 1 µm. Relevant for flotation deinking is, however, the particle size of the fragmented ink film after repulping. In conventional printing processes – letterpress, offset and rotogravure printing – the size of the ink particles ranges from 2 µm to 300 µm with the major range between 5 µm and 50 µm .9
The particle size of the fragmented ink film after repulping, as well as the particles’ hydrophobicity, are strongly dependent on the ink components, on the drying mechanism and, to a certain extent, on the interaction between ink and substrate. The basic components of the printing inks used on the conventional offset, flexographic, and rotogravure printing processes are ink vehicles, colorants (ink pigments or dyes), additives such as drying agents, and other components. The vehicle functions as a carrier (e.g. solvents) and as a binder (e.g. resins). The printing process and the requirements of the printer determine the selection of the components and their proportions. Table 1 shows the composition of conventional printing inks which are relevant for deinking.
Table 1. Composition of printing ink 10
Ink Components | Proportion |
---|---|
Vehicles – Carrier (e.g. solvents) – Binder (e.g. resins) | 10 % – 70 % 10 % – 70 % |
Colorants (pigment or dyes) | 5 % – 30 % |
Additives | 0 % – 10 % |
Fillers | 0 % – 10 % |
Conventional printing processes use inks with different compositions for technical reasons. Depending on the printing process, the ink’s consistency can vary from low viscosity to thick, elastic, and viscous. Carbon black has use for all types of black inks. The recipes are different especially for the amount and types of vehicles and additives. The ink manufacturer can make appropriate adjustments within these recipes to satisfy special requirements due to technical conditions and print substrates.
Binders in printing inks are partially responsible for forming the ink film. They encase the pigments, carry them across the inking and printing unit, and bind them firmly to the print substrate after the drying process.
Carriers in printing inks dissolve the solid binders and keep the ink in the press fluid. A dissolved binder in a carrier is a varnish or vehicle. This controls the consistency of the ink. After application of the ink to the substrate, the carriers should evaporate as much as possible without leaving a residue or penetrate into the substrate, allowing the binder to form a film. Some binders are based on renewable resources, and others are synthetic.
Carriers and binders differ greatly in their physical and chemical characteristics, depending on the printing process used to apply the resulting inks and the desired characteristics. Table 2 shows binders and carriers for different printing processes. The subdivisions of binders and carriers illustrate the variety of inks possible. The inks will obviously have different deinking characteristics.
Table 2. Binders and carriers for different printing processes 11
Printing Process | Binders | Carriers |
---|---|---|
Offset (coldset) | Hydrocarbon resin, Bitumen (for black inks) | Mineral oil |
Offset (heatset, sheetfed) | Drying oils Alkyd resin Phenol-modified colophony resin Hydrocarbon resins | Mineral oil |
Rotogravure | Colophony derivatives Hydrocarbon resins | Toluene |
Water-based flexography | Acrylic resins Maleic resins | Water (Alcohols) |
Important base materials among the natural ink binders are colophony (resin), asphalt and bitumen. Drying oils have a vegetable origin (linseed oil and soybean oil). They are produced from oil seeds with purification by refining. Alkyd resins and fatty acid alkyl esters are modified drying oils. Another natural base material for ink binders is cellulose.
Most synthetic binders are polymerisation products. Important synthetic binders are polyvinyl chloride, polyvinyl acrylamide copolymers, acrylic resins and hydrocarbon resins. For the water-based ink systems, which are becoming increasingly important, acrylic dispersions or saponified acrylic or maleic resins are used.
The most important carriers in inks are alcohols (isopropanol and ethanol), esters (ethyl acetate), glycols and glycol derivatives (methoxypropanol), ketones (acetone), hydrocarbons (mineral oils, toluene), and water. Table 3 shows the general influence of ink components on deinkability.
Table 3. Characteristics of ink components that influence deinkability 12
Characteristics of Ink Component | Deinkability “good” | Deinkability “poor” | |
---|---|---|---|
Pigment | Hydrophilic | x | |
Hydrophobic | x | ||
Alkali-resistant | x | ||
Not alkali-resistant | x | ||
Binder | Polar | x | |
Covalent | x | ||
Good cross-lingking | x | ||
Poor cross-linking | x | ||
Alkaline-soluble | x | ||
Alkaline-insoluble | x | ||
Poor pigment wetting | x | ||
Good pigment wetting | x | ||
Particle size | Small | x | |
Large | x |
The ink drying process is decisive for the binder and carrier to be selected and for the ink’s composition and deinkability of the printed product. The different types of drying are:
Physical drying of ink
-
- absorption of ink into an absorbent print substrate
- evaporation of the solvent
Chemical drying of ink
-
- oxidative drying
- drying by high energy radiation (UV curing radiation and electron beam curing).
Absorption and evaporation belong to the category of physical drying because no material changes occur except the absorption of carriers by the print substrate or evaporation of solvents into the air. Oxidative and high energy radiation drying belong to the chemical drying category. The binder molecules here become enlarged by oxygen uptake or polymerisation. Offset printing uses a combination of different drying methods as Table 4 shows. The contact of the ink film with the print substrate differs according to the drying process.
Table 4. Ink drying processes 13,14
Vehicles and Reactions | Drying Process | Printing Process | Subtrate |
---|---|---|---|
Drying oils, alkyd resins + oxygen | Chemical: oxidative polymerisation | Sheet-fed offset | Paper, board |
Mineral oils penetrate substrate | Physical: absorption | Offset (all variations) | Newsprint Uncoated paper Coated paper |
Mineral oils evaporate in special dryers | Physical: evaporation and part absorption | Web offset Heatset | Coated paper Uncoated paper |
Resins harden by radiation | Physical/ Chemical: oxidation comb. with absorption (IR drying) Polymerisation (UV drying) | Sheet-fed offset Web offset | Paper, board |
Solvent or water evaporates under heat or in air stream | Physical: Evaporation | Toluene-based rotogravure, Water- and solvent-based rotogravure and flexo | Paper, board |
Digital non-impact printing is advancing. It is no longer limited to office printing as in previous years. The technologies are now also used in direct mailing, personalisation and even for printing newspapers. Digital printing comprises two main groups, i.e. toner printing and inkjet printing processes, and the printed products behave completely differently in the deinking process.
After reading this chapter the reader should have a basic overview on the principle deinkability of printed products depending on printing process, printing ink fragmentation and chemical ink formulation.
Case
-
Five Continents Special Paper 450,000 tons packaging paper Project
-
The i-CTMP High Yield Pulping Production line of Shan Ying
-
Shandong Tianhe i-BCTMP pulping line upgrade project
-
Guangxi Sun Cultural Paper
-
Qianan Boda Cultural Paper
-
Vietnam Thuận An Paper PM8 Project
-
EG-Paper Packaging
-
400t/d Bamboo Fiber i-CTMP Project
-
Guangxi Kebao ZDG425 Drum Pulper
-
The Rebuild of IKPP OCC Line