The woodworking industries is a field with multiple branches, whose production is based on mechanical wood processing. The woodworking industries consist of the wood-based panel industry and its processing operations, the sawmill industry and its processed products, the construction carpentry industry, the furniture industry, the manufacture of wooden houses, the manufacture of wooden packages and other woodworking industry.
The theme focuses principally on the business environment, market and products for Finland’s two largest wood industry fields: the wood-based panel industry and the sawmill industry.
The sawmill industry accounts for roughly half of the gross value of the wood products industry, while the wood-based panels industry makes up approximately 10 per cent. The remaining gross value of the industry is attributable to processing. The wooden house and construction carpentry industries account for slightly more than one quarter and the furniture industry more than 10 per cent, while the remaining proportion is divided between the manufacturing of other wood products. 1
The woodworking industries employ a total of 30 000 people, of whom some 22 000 2 work in the manufacturing of sawn timber and wood products, and some 8 000 3 are employed in the furniture industry. Work is provided in all parts of the country.
First, thematic articles present the different applications of wood and questions related to wood construction from different perspectives. The articles cover, for example, the responsibility programme of companies engaged in the wood products industry and the sustainability principles followed in their operating environments.
Technological articles focus on innovation that helps to combat climate change, support the competitive wood industry and invest in the future. The assessment of climate impact highlights low-carbon construction through the use of wood products.
This article presents an overview of the manufacturing of wooden panels and sawn timber in Finland. The properties, use and production of different products are presented more closely in product-specific articles.
Wood panels and timber
One common feature of all wood panels is that they are made of wood through a gluing process. There is only a small amount of glue in wood panels. The least amount of glue, under 1 %, is used in hard fibreboard. Wood panels are made of veneer, chips, and fibre.
Veneer-based wood panels include plywood, LVL products and PSL products. Chips are used to make particleboard, LSL and OSB products, flakeboard and waferboard. Fibre material is used to make hardboard and softboard, as well as MDF, HDF, and LDF. This figure shows the division of raw materials in different products.
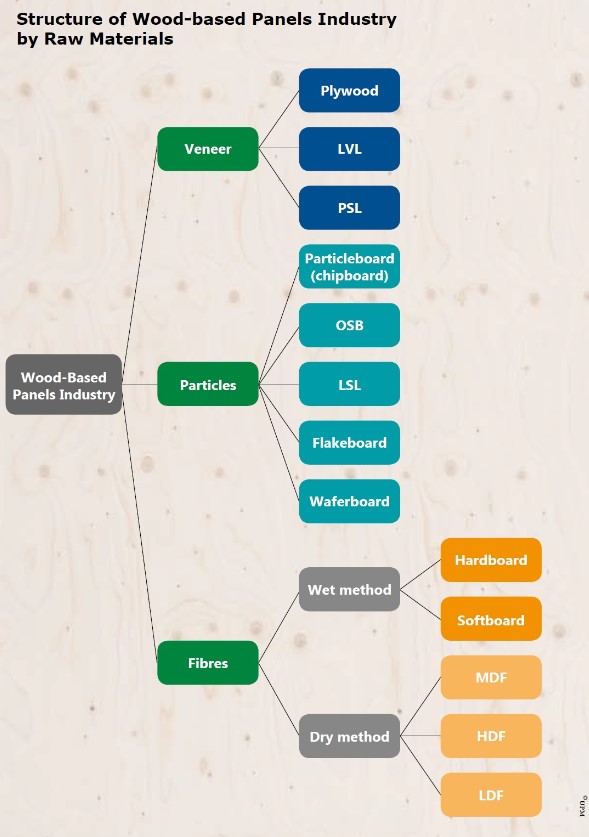
You can learn more in the following articles about plywood, LVL, particleboard, fibreboard and OSB, MDF, PSL and LSL panel products. More information on flakeboard and waferboard, noted in the figure, is available on ePuulevy site (OSB panel development).
Wood panel types that are made in Finland include plywood, LVL, particleboard and fibreboard. In Finland, there are ten plywood and LVL mills, four veneer mills, one particleboard mill and one fibreboard mill. The oldest branch is the plywood industry, which began on an industrial scale at Wilhelm Schauman’s mill in Jyväskylä, founded in 1912.
Processes in the wood-based panel industry are highly automated, making use of machine vision and robotics. This has been made possible by the machine manufacturing used by Finland’s plywood and LVL industry (see Innovations will help fight the climate change with wood products). 4
The sawmill industry is one of Finland’s oldest wood processing industries, alongside tar production. Finland’s first sawmills were in operation as early as the Middle Ages. Water-powered sawmills were converted to steam-powered mills in the 1860s, when the law changed to allow it. Currently, there are roughly 80 industrial sawmills in Finland. Three of them continue to operate on the same sites as the first 1870s steam-powered sawmills. 5
Finland’s sawmill industry capacity comprises independent sawmills that are owned by family businesses, and sawmills that are owned by forest industry groups, roughly in equal measure. There are also a number of local, small sawmills around the country.
Timber manufacturing has also rapidly developed its automated processes. Leaps in saw machine manufacturing include, among other things, the X-raying of logs, curve sawing, profiling, changeable drafts, machine vision-based classification, simulation tools and self-learning systems. The Rauma sawmill, which has been called the most modern and most efficient sawmill in the world, is set to begin operations in 2022 (read more at article: Rauma investment significant for entire sawmill industry). One of the latest sawing methods is the dx sawing method, which allows for even faster operation by using thinner blades. This method involves placing two double-axle saw units in tandem to work on the same cut. Learn more in the article an example of the newest sawmill technology.
Global market
Both the wood-based panel industry and the sawmill industry are important export businesses for Finland. The majority of both industries’ production is exported. Their market is global.
Over one million cubic metres of wood panels are produced every year. Plywood makes up over 90 per cent of the production volume. This makes Finland the largest plywood producer in Europe. The primary export countries are Germany, the United Kingdom and the Netherlands.
Finnish sawmills produce 11–13 million cubic metres of sawn goods per year. The volume is split 50/50 between pine timber and spruce timber. The primary export countries are Egypt, China, Japan, the United Kingdom and Germany. Asia has grown its share throughout the 2010s. Timber products were Finland’s 4th to 6th most important export in the later 2010s. 6
Further-processed wood products
Wood panels are shipped to customers as either coated or uncoated standard panels, or as further processed variants through the companies’ own sales offices or distributors. It is possible to ship semi-finished parts or ready-to-install components for different parts of the industrial and construction value chains, from subcontractors to end users. In the sawn timber market, customer-specific qualities and measurements have risen to the same level as standard-sized and standard-quality sawn timber goods.
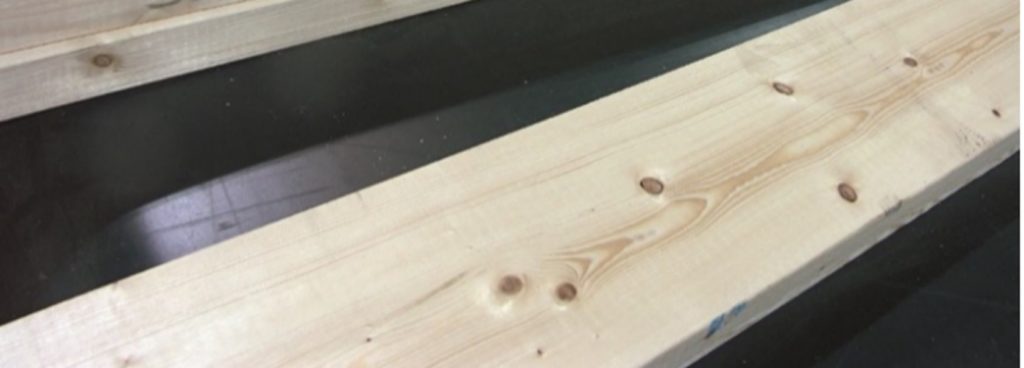
Timber is also used to make various refined products with established standards for size, quality and strength. This is a short showcase of primary further processed wood products that are made from timber. secondary further processed wood products include windows, doors, furniture and prefabricated wooden houses. 7
Planed and painted goods
All-round planed sawn timber is a type of smooth timber that has had each of its sides planed by around 2 mm. Profiled planing is used to achieve the desired timber profile. Shape-planed products include exterior and interior cladding boards, panels and floorboards.
The profile type determines the kind of seam that is formed when the planed product is installed. The profile can be straight, chamfered, rounded or weatherboard, for example. Profiled batten strips include baseboards, skirting boards, mouldings and various boards for the walls and the ceilings.
Planed goods can be shipped either with a wood surface or with a surface coating. Exterior cladding boards, panels and batten strips are available with either a base paint, or with both base and surface paint. In addition to paint, surface treatment may be carried out with wax or lacquer.
Finger-jointed timber
Timber can be extended with a finger joint, which makes it possible to produce the desired length and quality of timber. For instance, furniture and window sashes are applications of finger-jointed, knotless timber, made by cutting off sections with knots and joining the knotless pieces together with glue and a finger joint.
Strength-graded timber
Structural timber is required to be strength-graded. Strength grade labels are stamped on the side of each timber piece. The stamp shows the standardised strength grade and dimensions.
The strength grade is influenced by the amount and location of knots in the timber as well as other faults, such as cracks and twisting. Strength grading is generally carried out by machine, but visual grading can also be performed by a person with a valid strength grading qualification.
Glulam boards
Solid wood glulam boards are made from planed and splitted timber by gluing the pieces’ sides together to form a panel. These panels are used by the furniture industry to make shelves and desktops.
Glulam beams
Glulam beams, glue-laminated timber (GLT) is a solid wood product made from lamellas that is intended to be used in load-bearing structures. GLT has a maximum height of about 2 metres and a maximum length of around 30 metres.
Lamellas in direct supports are generally 45 mm thick. Thinner lamellas are used in bendable parts. GLT is generally shipped all-round planed. Its primary applications are columns and beams in business, industry, sports facilities and agricultural construction.
Cross-laminated timber
Cross-laminated timber (CLT) is a solid wood panel that is made of timber layers that are glued together in a crisscross pattern. There is an odd number of panel-like timber layers. Cross-laminated timber is a strong and stiff material that remains lightweight.
CLT panels are used in building walls and floors as load-bearing and stiffening structures. It is also possible to make entire exterior wall structures from CLT, in which one panel forms the load-bearing structure, insulation layer as well as exterior and interior surfaces. The product is also suitable for use in facility element production as a frame structure. CLT is also called KL-trä (korslimmat trä), X-Lam and KLH (Kreuzlagenholz).
Nail plate products and I-beams
Roof trusses, frames and beams are referred to as nail plate products when the joints are carried out with steel nail plates. The spiked nail plate is pressed precisely onto the joint parts, which are specified in the drawings.
I-beams consist of wooden supports and a slim web plate, which may be made of plywood or fibreboard, among other things. I-beams are used as beam structures for lofted ceilings, base floors, and intermediate floor beams.
Strength-graded timber must be used in load-bearing nail plate structures and I-beams.
Heat-treated timber
It is possible to modify timber thermally, the process of which is based on high temperatures (180–230 °C) and steam. No chemicals are used in the manufacturing process. Products made with the patented Thermowood® thermo-treatment method are called Thermo-S (Stability) or Thermo-D (Durability).
Thermo treatment aims to improve the wood’s weather and rot resistance properties. Thermally modified wood will also have a less pronounced moisture movement compared to untreated timber. Thermally modified wood is generally used in sauna interiors, external cladding, terrace structures and fences, among other things.
Pressure impregnation
Timber and wooden poles may be pressure-impregnated by using rot and blue-stain prevention agents. This process takes place in an impregnation cylinder, using pressure and water with standardised quality control.
Finnish pressure-impregnated timber is generally rated A or AB for its protection class. A-class timber is generally used in structures that are in contact with the ground, water or concrete. Timber that is 48 mm thick or more is treated in accordance with A-class requirements. AB-class timber is intended for aboveground structures.
Log structures
Logs are the oldest material used for wooden buildings, having been in use for over 1 000 years. Today’s industrial log production enables the manufacture of a variety of log structures. Glued laminated logs, planed logs made to a profile, and round logs are in use. Hand-crafted logs are also available.
Generally, the log construction industry uses glued laminated logs, which has the benefits of having larger dimensions as well as lower cracking and sag than natural wood. Planed logs and round logs are generally used for more modest leisure buildings.
Source weblink: https://forestbiofacts.com/wood-products/woodworking-industry/
Case
-
Five Continents Special Paper 450,000 tons packaging paper Project
-
The i-CTMP High Yield Pulping Production line of Shan Ying
-
Shandong Tianhe i-BCTMP pulping line upgrade project
-
Guangxi Sun Cultural Paper
-
Qianan Boda Cultural Paper
-
Vietnam Thuận An Paper PM8 Project
-
EG-Paper Packaging
-
400t/d Bamboo Fiber i-CTMP Project
-
Guangxi Kebao ZDG425 Drum Pulper
-
The Rebuild of IKPP OCC Line